PLC and MotionControl integrated in one IEC 61131-3 Development System
Everything from single to multi-axis movements to CAMs can be developed together with the logic application directly in the familiar IEC 61131-3 programming environment. A motion controller with CODESYS SoftMotion implements the motion functionality in form of a tool kit integrated in the PLC Development System.
The Runtime System CODESYS Control SoftMotion has to be implemented on a motion controller in order to be able to program it with the CODESYS SoftMotion tool kit.
Platform requirements:
- has to be supported by CODESYS Control (recommended min. 32 bit with FPU).
- needs sufficient performance for the calculation of the position, velocity and acceleration data.
- needs hard real time properties with low jitter values.
When working with CODESYS SoftMotion controllers the user has many different options when it comes to implementing his motion tasks. For example, he can make use of the provided certified PLCopen motion POUs and appreciate the full functionality of the IEC 61131-3 Development System.
Here you find further information about CODESYS SoftMotion CNC+Robotics.
CODESYS SoftMotion contains
- Certified PLCopen POUs for single and multi-axis movements
- Certified PLCopen POUs for add-on functions like diagnostics, stop, CAM controller
- Additional POUs for different tasks like monitoring dynamic data or following error, operating CAMs and CAM controllers
- Visualization templates to quickly and easily commission the POUs using the CODESYS visualization
- Visualization elements which make it possible to change the CAMs and the CAM controllers online
- Integrated graphical CAM editor with extensive configuration options
- Virtual and logical axes supported
- Integrated drivers for numerous CAN, CANopen® and EtherCAT® drives
- Configuration of the drives as standard field devices
- Example CODESYS SoftMotion projects
Product for device manufacturers
CODESYS SoftMotion Runtime Toolkit:
Toolkit for implementing CODESYS SoftMotion on systems with sufficient performance such as powerful embedded devices and PLCs (FPU recommended) or based on industrial PCs
Typical Applications
- Pick&Place Application:
Using PLCopen POUs to position (pick) and belt-synchronously place an object on a moving target, visualizing the process with the appropriate visualization templates - Labelling / CAM Application:
CAM editor, PLCopen POUs and virtual axis used as king pin, various visualization templates, CANopen servo drives, touch probe / latching functionality - Injection Moulding Machine:
Realized with PLCopen POUs and other SoftMotion-specific functions such as on-the-fly switching from position control to torque control.
Overview of the supported drives
CAN/CANopen
- Bonfiglioli® iBMD
- CMZ® BD, SD, LBD
- Festo® EMCA, CMMP
- Generic CiA® 402 driver (also for multi-axis drives)
- Infranor® cd1-k, XtrapulsPac
- JAT ECOVARIO®
- KEB® F5, Stepless Technology
- Metronix® ARS 2000 series
- Nanotec® PD4C
- Schneider Electric™ Lexium05, Lexium23, Lexium28, Lexium32, Lexium32i and SD-3
Sercos®
- Bosch Rexroth IndraDrive C/M/Cs/ML/Mi
EtherCAT
- Beckhoff® EL2521, EL5101, EL72x1, EL703x, EL704x
- Bonfiglioli iBMD
- Bosch Rexroth® ctrlX Drive CoE
- Bosch Rexroth® IndraDrive CoE (Start-up Documentation)
- CMZ BD, LBD
- Control Techniques™ Digitax, Mentor and Unidrive
- Copley® Accelnet
- Delta® ASDA A2, A3, B3
- Delta R1-EC5621
- Festo CMMP EtherCAT
- Generic CiA 402 driver (also for multi-axis drives)
- Generic SoE driver (also for multi-axis drives)
- Hitachi® ADV series
- Infranor XtrapulsPac
- JAT ECOVARIO
- KEB F5, H6
- KEBA® KeDrive D3
- Kollmorgen AKD®, AKD Servodrive, AKD-N/C, MKD-N/C, AKD2G
- Metronix ARS 2000 series
- Omron® G5
- Nidec® Unidrive M
- Panasonic® MINAS A5B, A6B
- Parker® compax3, SBC, PSD
- Sanyo Denki® RS2
- Schneider Electric Lexium32, Lexium32i
- Servotronix® CDHD
- Stäubli® uniVAL
- Stöber POSIDRIVE®, SD6, SI6/SC6
- WEG SCA06
- Yaskawa® Sigma7 series
Howtoget
- You are a system integrator or a user in the machine/plant construction sector or the like:
All you need is a controller already equipped with CODESYS SoftMotion. Millions of CODESYS-compatible single devices and over 1,000 different device types from more than 500 manufacturers offer you a large range of hardware for your automation projects. CODESYS Inside offers a selection of manufacturers that offer CODESYS-compatible devices. Or simply implement your own PC-based motion controller by installing the SoftPLC CODESYS Control RTE (under Microsoft Windows) or CODESYS Control (for example under Linux®) on your IPC. - You are a manufacturer of programmable devices:
Get the CODESYS Runtime Toolkit and implement your own customized motion controller with CODESYS SoftMotion. You can choose from a range of different combinations when selecting the CPU platform and the operating system for your motion control system.
Products
Logic control and motion integrated in one single IEC 61131-3 system: Development kit for everything from basic motion applications to advanced CNC and robotic controllers.
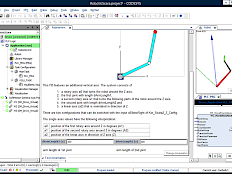
SoftMotion CNC+Robotics
3D-CNC motion control for motion controllers with complete 3D-CNC and robot functionality, including an interpolator and kinematic transformations, integrated in the IEC 61131-3 programming system.