Webinar OPC UA & CODESYS
The webinar provides you with an overview of the comprehensive solutions CODESYS offers around OPC UA, and how you can benefit directly from them. Key topics are OPC UA Server/Client, OPC UA PubSub and user-defined information models (Companion Specifications).
Contents:
00:00 Welcome
00:22 Introduction
03:37 Communication between PLC and visualization | OPC UA Server/Client, OPC UA Information Models, method calls, HMI
27:34 Server/client communication between controllers | OPC UA Server/Client, Data Sources Manager
36:34 Communication between arbitrary devices | Network Variables, OPC UA PubSub
46:36 Recap
Platform Independent Standard Access to Variable Data
OPC UA (Unified Architecture) is a new development of OPC specifications which allows not only for transportation of machine and plant data but also for a semantic description of these data in a machine-readable way. OPC UA is a platform independent standard based on TCP. The protocol stack is available for all members of the OPC Foundation. The OPC UA specification provides different profiles for the scaling of individual features.
Overview CODESYS OPC UA Server
- Implementation of the communication according to the OPC UA specification using the profile "Micro Embedded Device Server", based on the communication stack of the OPC Foundation
- Additional component to the CODESYS Control Runtime System for device manufacturers as an option to the CODESYS Control Runtime Toolkit. Implementation in all device platforms supported by CODESYS with sufficient performance, as well as existing TCP/IP stack and real-time clock.
- Included without additional license fees as a limited version in all application-based runtime licenses
- Provision of data via the symbol configuration in the CODESYS Development System.
Alternatively: Provision of data in different symbol groups with specific user rights in a communication manager object. - Communication with any OPC UA clients
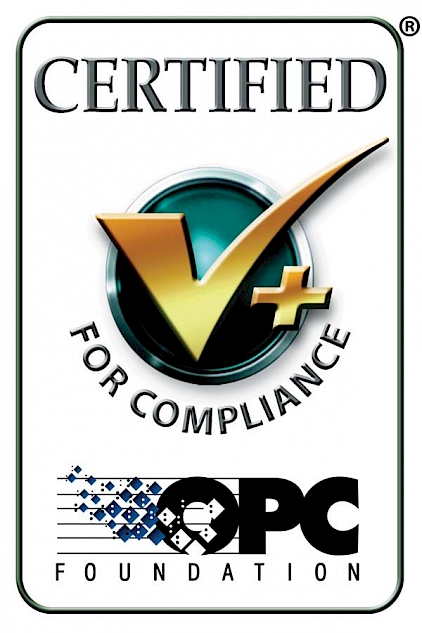
Overview CODESYS OPC UA Client
- Additional component to the CODESYS Control Runtime System for device manufacturers as an option to the CODESYS Control Runtime Toolkit
- Enables implementation of different clients in all device platforms supported by CODESYS with sufficient performance, existing TCP/IP stack, and real-time clock
- Support of all available functions in CODESYS OPC UA Server
- Usage variants for reading in data for the IEC 61131-3 application and CODESYS visualization:
- Explicit call of library functions within the application
- Convenient configuration in the data source manager
Overview OPC UA PubSub
- CODESYS library for data exchange according to the standardized procedure between devices via UDP protocol
- Use of function blocks for sending (Publisher) and receiving (Subscriber) the data as well as for configuring the communication in the PLC application
- Execution of the blocks cyclically in a PLC or background task
- Diagnostic information for almost all functions can be queried at runtime or via visualization
- Supplied example project for an easy start
- Extensibility for future protocols as well as TSN/FLC
- Licensing per device ("SL" license)
- System requirements on the controller:
- Implemented system library for socket access to Ethernet
- Possibility of license storage (via dongle or software container)
- Can be used in all CODESYS SoftPLCs (see CODESYS Store)
Further information and purchase in the CODESYS Store.
Howtoget
As a system integrator or a user in the machine or plant construction sector or the like:
- Use controllers that are already equipped with CODESYS OPC UA Server/Client.
- Obtain SoftPLC systems from the CODESYS Store that already include CODESYS OPC UA Server/Client or that can be conveniently relicensed.
- For controllers with integrated SysSocket library and license container or SoftPLCs from the CODESYS Store: Install and license CODESYS OPC UA PubSub SL for standardized data exchange.
As a manufacturer of programmable devices:
- Purchase CODESYS OPC UA Server/Client and implement the supplied additional components into your device using the CODESYS Control Runtime Toolkit.
- Provide the license container so that your customers can re-license CODESYS OPC UA Server/Client or OPC UA PubSub themselves if required.
Advice, offer, and further information through info@emea.com.tr
Products
CODESYS offers seamlessly integrated communication protocols for a wide variety of interfaces and requirements.
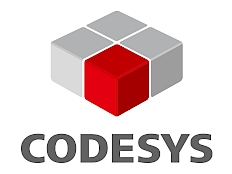
OPC Server
Standard Interface to access the IEC 61131-3 process data of a controller via Open Platform Communications.
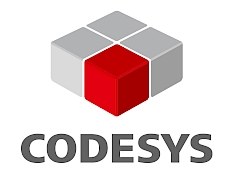
PLCHandler
Compact software interface (API) for easy access to the PLC variables in CODESYS controllers from external systems
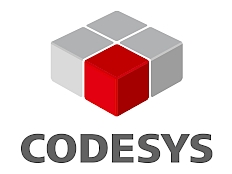
BACnet
Configurator and protocol stack fully integrated in the IEC 61131-3 Development System
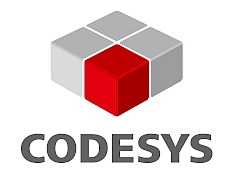
Serial interfaces
Although today almost every industrial controller has an Ethernet connection, serial interfaces are still installed in many industrial devices. This allows, for example, for the connection of appropriately equipped sensors and actuators or extensions.
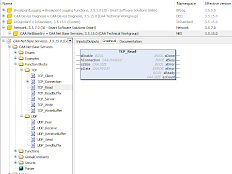
Standard Ethernet
How does CODESYS communicate via Ethernet? How can I send and receive data from a CODESYS-compatible PLC via TCP or UDP? How can I realize data exchange from the PLC application?
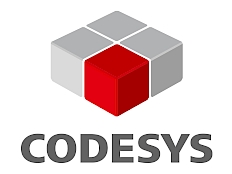
Fieldbus systems and Industrial Ethernet
Sensors and actuators/actuators for processing control tasks can be separated from the controller via fieldbus and Ethernet systems with industrial communication protocols.
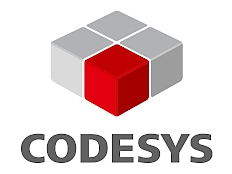
IIoT libraries
All IoT communication protocols can be implemented and used on different transmission media via software.
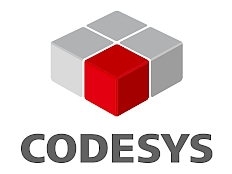
Other communication options
If a physical port is available on a controller, communication protocols can usually be implemented simply via software, either as part of the IEC 61131-3 control application or as separate library modules. Data exchange is performed by explicitly calling functions or function blocks as part of the logic control.
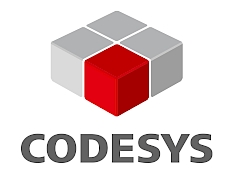
Proprietary communication protocols
CODESYS supports the most common standard communication protocols for data exchange between controllers, such as OPC UA. In addition, Ethernet-based fieldbus systems such as PROFINET or EtherNet/IP™ make it easy to exchange data between controllers by implementing master and slave functions.